Nachhaltigkeit ist mittlerweile auch im Sportswear-Markt angekommen. Konsumierende sehnen sich nach funktionalen Produkten mit nachhaltigen, langlebigen und hochwertigen Materialien. Viele Marken versuchen, die Lücke zwischen Mode und innovativ-funktionalem Design zu schließen.
In Sportbekleidung lauern oftmals giftige Chemikalien
Eine der größten Herausforderungen in Sachen Sportbekleidung: Je funktionaler die Kleidung sein soll, desto komplexer ist die Herstellung. Das Problem liegt vor allem darin, dass die Funktion der Produkte oftmals durch gesundheitsschädliche Chemikalien gewährleistet wird.
Giftige Chemikalien schaden Mensch und Natur. Sie werden nicht nur von Textilbeschäftigten während des Herstellungsprozesses eingeatmet, sondern können im schlechtesten Fall auch von Endverbraucher*innen über die Haut aufgenommen werden. Landet die konventionelle Sportbekleidung auf Mülldeponien, wird sie nicht biologisch abgebaut – giftige Restchemikalien gelangen in den Boden oder lokale Gewässer und werden von Menschen und Tieren aufgenommen.
Die Sportbekleidungsindustrie steht dementsprechend vor großen Herausforderungen, Produkte zu entwerfen, die nicht nur nachhaltig und/oder kreislauffähig sind, sondern auch gesund für Mensch und Umwelt. Auch deswegen erleben wir eine Ära voller Innovation und Veränderungswillen.
Der Großteil der Sport- und Outdoorbekleidung wird immer noch außerhalb Europa produziert
Die größten Sportmodeunternehmen produzieren den Hauptteil ihrer Produkte immer noch außerhalb Europa. Die wichtigsten Produktionsländer sind beispielsweise Vietnam, Indonesien, Kambodscha und China. Der Einsatz giftiger Chemikalien ist in diesen Ländern jedoch nach wie vor weitgehend nicht reguliert. Die oftmals langen und unübersichtlichen Lieferketten machen die Rückverfolgbarkeit der verwendeten Chemikalien nahezu unmöglich.
Lokale Textilproduktion als Nachhaltigkeitsstrategie
Wie der Weg hin zu einer transparenten und ressourcenschonenderen Outdoorindustrie gehen kann, zeigt uns Löffler – ein österreichisches Label, das nun mittlerweile seit über 50 Jahren in der Sportbekleidungsbranche aktiv ist. Das Unternehmen ist sich in dieser Zeit immer treu geblieben: Der Großteil der Produktion – von der Strickerei über Produktentwicklung, Design, Zuschnitt, Konfektion, Näharbeiten, bis hin zur Endkontrolle und dem fertigen Kleidungsstück – findet weiterhin größtenteils in Österreich statt, am Unternehmenssitz in Ried im Innkreis. Lediglich bei den Näharbeiten werden sie vom Tochterunternehmen in Bulgarien und weiteren Lohnpartnern in Europa unterstützt. Die Materialien werden von Lieferanten aus Europa bezogen.
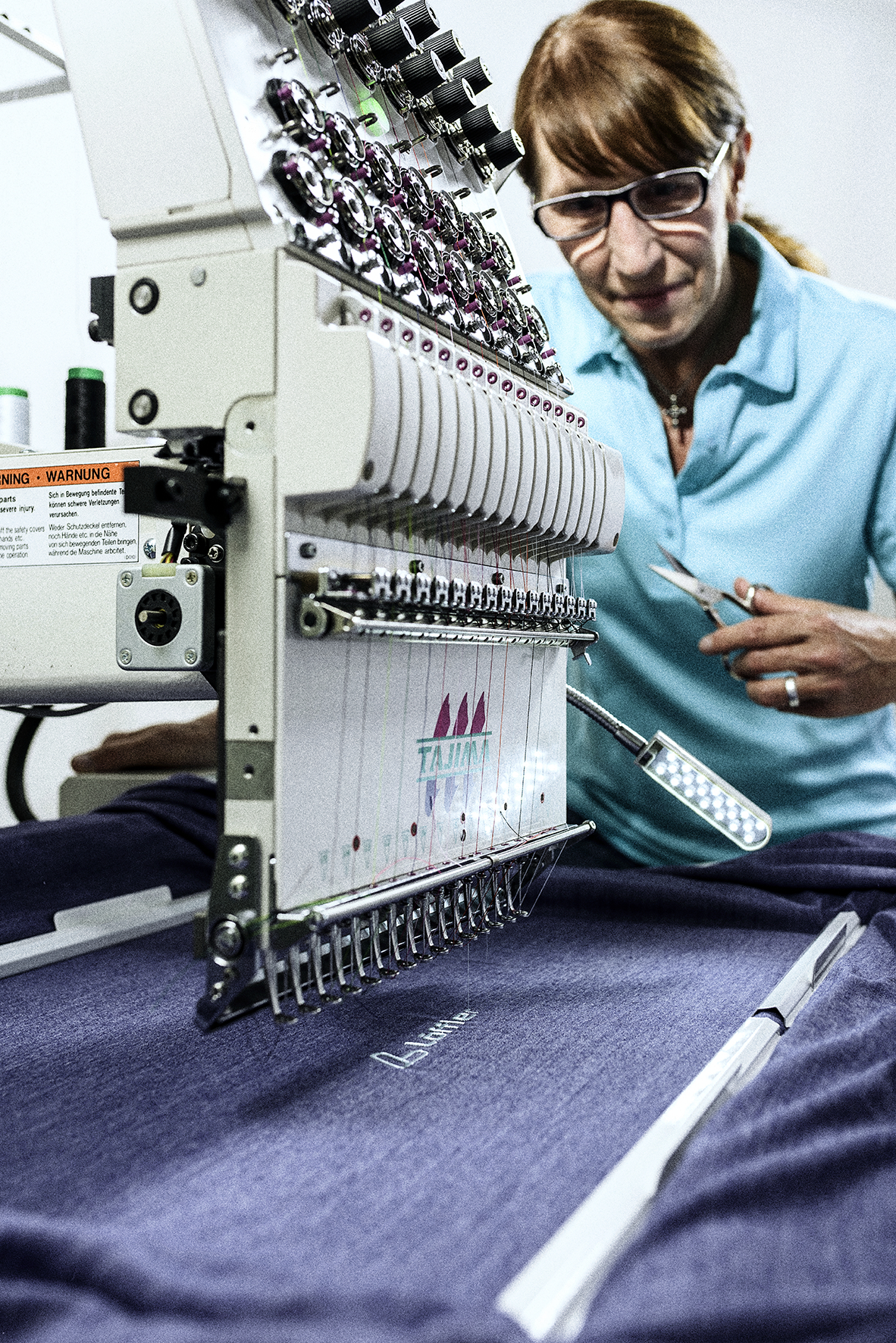
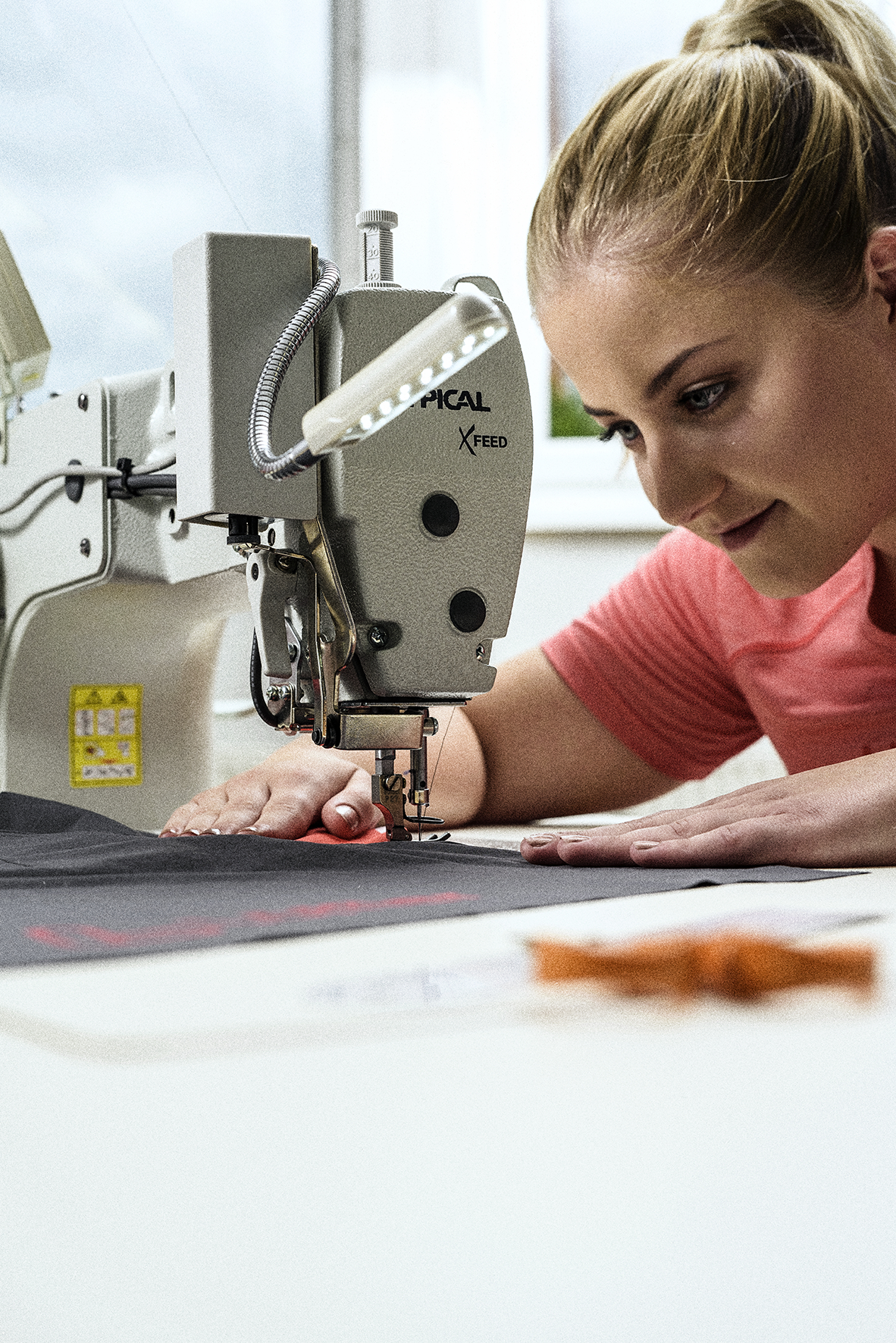
Die Marke zeigt damit: Innovative und hochqualitative Sportbekleidung kann durchaus auch regional hergestellt werden kann – ohne dabei Kompromisse in Sachen Unternehmensverantwortung und Nachhaltigkeit einzugehen. Als Hauptproduzent der eigenen Sportbekleidung kann Löffler die Produktion gezielter angehen. Materialien, Chemikalien und Herstellungsverfahren, die ökologisch oder gesundheitlich umstritten sind, werden beispielsweise nicht eingesetzt beziehungsweise durch Alternativen ersetzt.
Ihre zwei Säulen, so das Unternehmen selbst, seien Performance und Verantwortung. Es erkennt, dass beide Bereiche das Potenzial haben, sich als Unternehmen ständig weiterzuentwickeln. Sei es Innovation und Materialentwicklungen im eigenen Haus oder die Optimierung sozialer und ökologischer Aspekte entlang der Lieferkette – die Marke setzt sich regelmäßig mit den Themen auseinander.
2020 hat Löffler deshalb erstmals einen Nachhaltigkeitsbericht veröffentlicht. Ziel war es vor allem Argumente für eine lokale Textilproduktion mit belastbaren Daten zu hinterlegen. Dabei sind teilweise auch überraschende Fakten aufgekommen: Das Unternehmen war sich beispielsweise selbst nicht bewusst, wie viele Tonnen Abfall (größtenteils Kartonagen) intern entstehen. Es zeigt damit, dass Selbstreflexion und -kritik zu einer verantwortungsbewussten Unternehmensführung dazugehören. Die eigenen Herstellungsprozesse müssen stetig hinterfragt und verbessert werden.
Wir haben uns mit Produktentwickler Dominique Roshardt und Marketingleiter Jörg Tichy von LÖFFLER unterhalten und darüber gesprochen, wie Materialentscheidungen getroffen werden, welche Vorteile moderne Technologie in Sachen Stoffentwicklung bietet, an welche Grenzen das Unternehmen in Sachen Nachhaltigkeit stößt und warum vor allem Zeit ein wichtiger Faktor bei Veränderungsprozessen ist.
Löffler produziert einen Großteil seiner Stoffe in der hauseigenen Fabrik in Österreich. Woher rührt diese Entscheidung?
Löffler: Die lokale Produktion bietet allerlei Vorteile, erfordert aber auch viel Know-how und Erfahrung. Allein bei der Materialentwicklung können die Stoffe viel präziser auf die jeweilige Funktion abgestimmt und ausgerichtet werden. Anpassungen, die sich durch die Qualitätssicherung und die Praxistests als notwendig erweisen, können auf kurzem Weg umgesetzt werden. Durch dieses ausgeprägte Verständnis für Materialien profitieren auch nachgelagerte Schritte. Das ermöglicht uns größere Unabhängigkeit. Wie effektiv dieser Prozess ist, hat sich beispielsweise bei unserem Material hotBOND® gezeigt. Dafür wurden wir sogar mit dem Preis für Innovation des Landes OÖ 2018 ausgezeichnet.
Mit der von Löffler entwickelten und patentierten hotBOND®-Technologie werden hochelastische Materialien mittels Ultraschall punktuell zu ultraflachen Verbindungen verschweißt.
Das bedeutet: keine Nähte, die drücken oder scheuern. Die nicht-genähten, sondern verschweißten Verbindungen sind extrem reißfest, so elastisch wie das Material selbst und ultraflach. Sie gewährleisten damit maximale Bewegungsfreiheit ohne Druck- oder Scheuerstellen.
Neben Fahrradhosen in verschiedenen Längen sowie als Bund- oder als Trägerhose wird die hotBOND® Technologie auch bei Bike-Trikots angewendet. Außerdem ist das innovative Material in der Running- und Outdoorkollektion erhältlich. Die Herstellung und Fertigung der hotBOND® Kollektion erfolgt ausschließlich am Firmenstandort Ried im Innkreis, Österreich.
Mit hotBOND® reflective setzt Löffler noch eins oben drauf und verspricht reflektierende Kleidung, die ohne Lichtanstrahlung sehr dezent und unauffällig ist. Erst wenn das Material angestrahlt wird, reflektiert dieses.
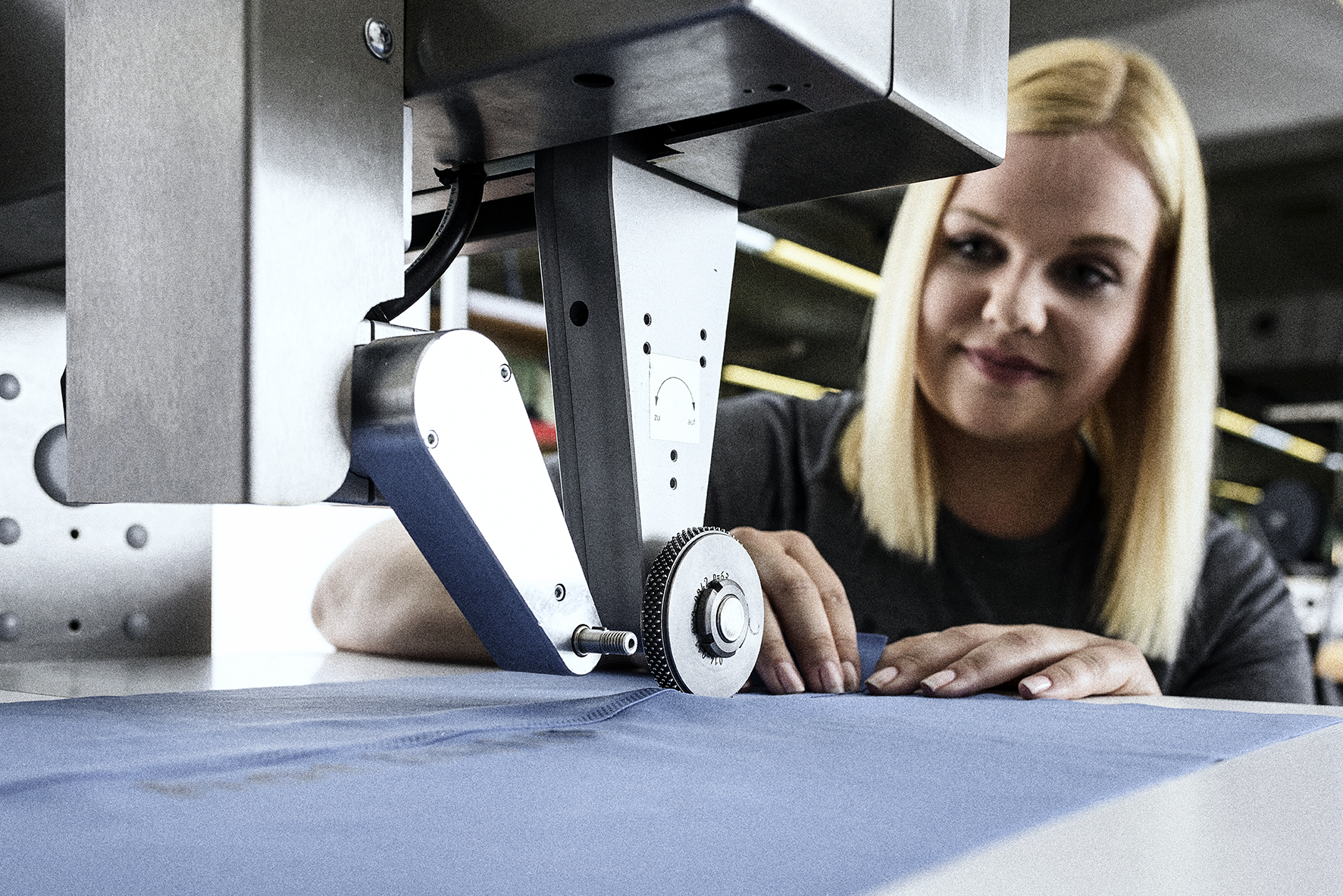
Sportbekleidung muss besonderen Anforderungen gerecht werden, wind- und wetterfest, atmungsaktiv oder temperaturregulierend sein. Welche Herausforderungen bringt das im Entscheidungsprozess für ein Material mit sich?
Die Entscheidungen fallen bereits beim Sourcing beziehungsweise bei der Entwicklung des Materials. Wir orientieren uns dabei am geplanten Einsatzbereich, von dem wir Anforderungen an das Material ableiten. Sobald die Kriterien definiert und festgelegt sind, wird das entsprechende Material gesourct.
Dann folgt die Qualitätssicherung. Zu den Qualitätstests gehören unter anderem der Waschkrumpf (Anm. d. Red.: dient zur Bestimmung und Bewertung der Maßänderung von Textilien beim Waschen und Trocknen), Abriebtests (Martindale-Test, Anm. d. Red.: Beständigkeit des Gewebes gegenüber anderen Materialien bei wiederholter Reibung mit anderen Materialien), Spraytests (Anm. d. Red.: Bestimmung der wasserabweisenden Eigenschaften) und die Roll-Neigung. Besteht das Material die ersten Qualitätstests, werden – je nach Kapazität und aktueller Auslastung der Produktion – Prototypen beziehungsweise Testartikel herstellt. Daraufhin erfolgt der Praxistest. Hier steht ein Pool an Testpersonen zur Verfügung, die die neuen Produkte in den jeweiligen Sportarten und Einsatzbereichen testen.
Die Ergebnisse aus der Qualitätssicherung, die Abstimmung mit der Entwicklungsabteilung und das Feedback der Produkttester*innen werden anschließend zusammengeführt und ergeben ein Gesamtbild. In die finale Entscheidung fließen zudem der Preis des Materials und eine Produktkalkulation ein. Stimmen Haptik, Optik, Qualität, Funktion und der Preis übereinander, wird das neue Material in die Kollektion übernommen.
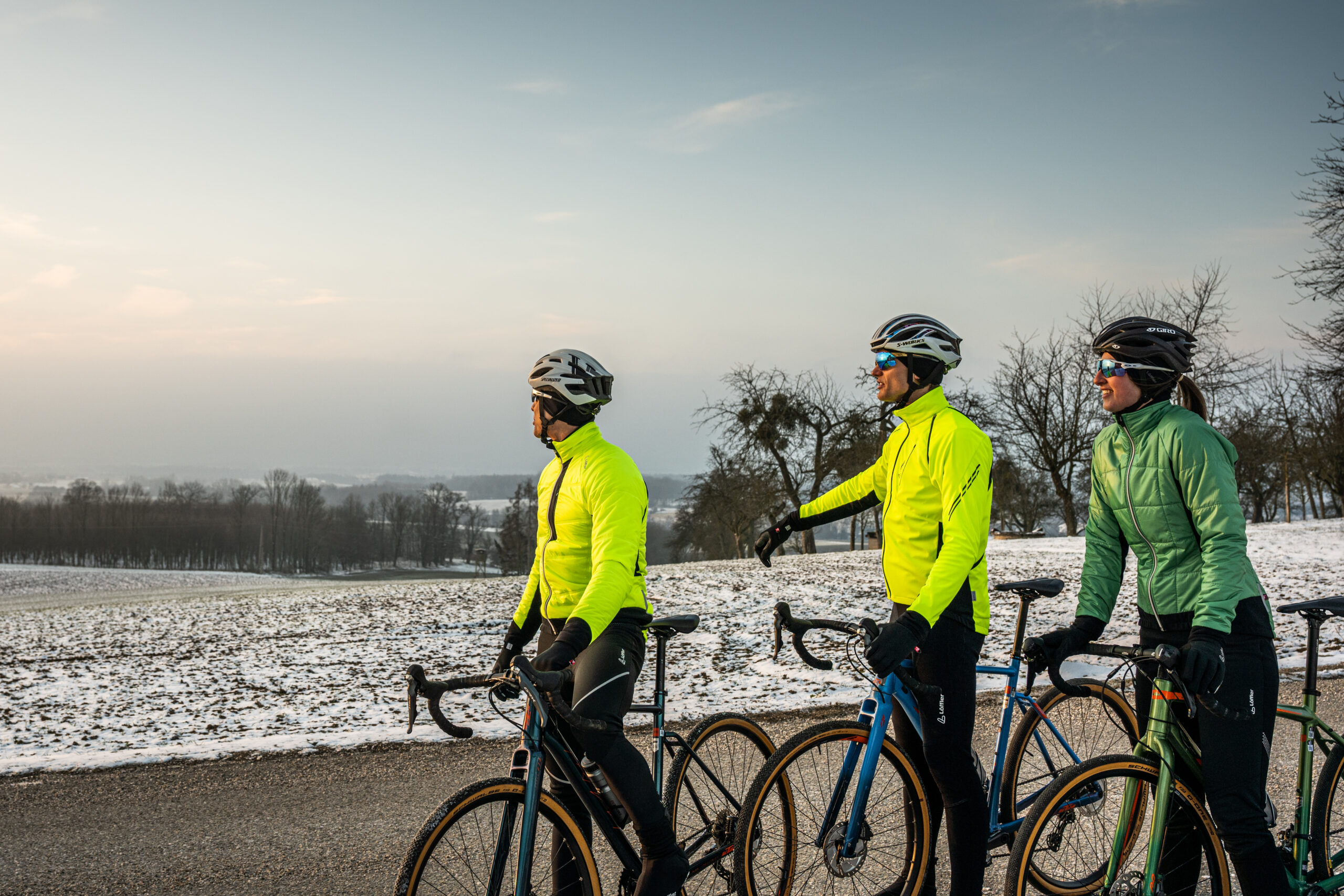
Bei Regenjacken zum Beispiel setzen wir auf PFC-freie Wasserabweisung. Derzeit ist nur noch eine Qualität im Einsatz, bei der das noch nicht der Fall ist – der Rest ist bereits umgestellt. Mittelfristig wird diese aber auch auf PFC-freie Imprägnierung umgestellt.
Dieser Prozess bezieht sich nicht nur auf Produktneuheiten und Materialentwicklungen. Jeder Stoff und jedes Material, das bei Löffler verarbeitet wird – egal ob in der hauseigenen Strickerei oder einem unserer Partnerunternehmen – wird bei Wareneingang überprüft, analysiert und dementsprechend für die Produktion aufbereitet. Durch die Einhaltung dieser strengen Auflagen wird eine durchgängige und hohe Qualität gewährleistet.
Als Produzent haben wir den Vorteil, dass wir schon bei der Materialauswahl anzusetzen können. Wenn wir uns hier für hohe Qualität entscheiden – auch bei Accessoires wie zum Beispiel Reißverschlüssen – dann wissen wir, dass das Produkt langlebig ist. Da wir das Bekleidungsstück auch inhouse genäht haben, wissen wir, wie wir es später reparieren können.
Bei welchen Entscheidungen stoßt ihr in Sachen Performance an Grenzen?
Grenzen zeigen sich, wenn sich völlig neue oder erweiterte Produktanforderungen ergeben. Das ist beispielsweise der Fall, wenn ein bestehendes Material aufgrund der neuen oder erweiterten Anforderungen eine besonders hohe Abriebfestigkeit aufweisen soll, jedoch nicht dafür entwickelt wurde. Die Herausforderung dabei ist, zu entscheiden, ob mit dem bisherigen Material weitergearbeitet werden kann oder eine neue Materialkomposition notwendig ist.
Wie können wir uns diesen Prozess vorstellen?
Hier ein Beispiel: Eine ursprünglich geplante Midlayer-Qualität ist für den Bereich Running konzipiert worden. Jetzt soll sie auch für Produkte in einem anderen Einsatzbereich dienen, bei dessen Ausübung oftmals ein Rucksack getragen wird (wie etwa beim Wandern oder Skitouring). Da die Träger des Rucksacks aufliegen, entsteht Reibung – das Material „fusselt“ an den Reibungspunkten. Die Materialanforderung in diesem Fall wäre also eine besonders hohe Abriebfestigkeit – eine erweiterte Anforderung, die vom bisherigen Anspruch an das Material abweicht.
Woher bezieht ihr die Rohstoffe für die Textilien?
Aufgrund unserer regionalen Verortung liegt hier der Fokus auf Materialien aus Europa. Auch hier zeigt sich der Vorteil von Produktion und Produktentwicklung am Firmensitz in Ried. Denn: So kann auch die Entwicklung eines Materials, das bisher nur in außereuropäischen Ländern verfügbar ist, wieder nach Europa (oder spezifisch nach Österreich) geholt werden.
Textillaminat kann aktuell beispielsweise nur aus Asien bezogen werden. Unsere hauseigene Alternative dazu ist transtex®SHELL, das wir in Zusammenarbeit mit dem österreichischen Unternehmen Voack 3,5 Jahre lang entwickelt haben. Dabei handelt es sich um das erste, zu 100 Prozent in Österreich hergestellte – dreilagige – Softshell (Anm. d. Red.: mehrschichtiges Material, das Feuchtigkeit besonders gut transportiert). Mit dieser Innovation steht Löffler ein regional hergestelltes Textillaminat zur Verfügung, das winddicht, atmungsaktiv, wasserabweisend und PFC-frei imprägniert ist.
In Sachen Isolation arbeiten wir mit PrimaLoft®, ein aus Deutschland stammendes Material. Die Elastik- und Fleece-Stoffe kommen aus Italien. Die Webstoffe kommen aus Frankreich und aus preisstrategischen Gründen auch aus Asien. Damit künftig die verwendete Wolle beziehungsweise die Kammzüge nachverfolgt werden können, arbeitet Löffler ab 2022 mit dem Responsible-Wool-Standard-Zertifikat. Die Kammzüge werden aktuell aus Australien, Neuseeland, Südamerika und Südafrika bezogen.
Zudem haben wir uns als Ziel gesetzt, im kommenden Jahr mehr recycelte Garne abzumustern. Bei positivem Feedback in Sachen Qualität und Performance werden wir diese in der Produktion aufnehmen. Ziel ist es, bis 2022/2023 einen Recyclinganteil der Strickgarne aus synthetischen Polymeren von 3,3 Prozent zu erreichen – gemessen nach Gewicht, entspricht das circa drei Tonnen.
Ihr setzt in Sachen Stoffentwicklung vor allem auf moderne Technologie. Welche Vorteile ergeben sich daraus?
Moderne Produktionsmittel und Verfahren sind unseres Erachtens notwendig, um die Kollektion weiterzuentwickeln. Ein wesentlicher Vorteil bei Löffler besteht darin, innovative und effiziente Technologien mit den jahrzehntelangen Erfahrungen in den angebotenen Sportarten zu kombinieren. Ein Beispiel dazu ist unser hochmoderner Cutter im Stoffzuschnitt. Mit einem Programm im Hintergrund können wir gewährleisten, dass so wenig wie möglich Verschnitt produziert wird. Denn dank der modernen Technologie dieses Cutters können Schnittbilder auch mit minimalem Abstand angelegt werden. So arbeiten wir ressourcenschonend mit effizienten Schnittlagenbildern.
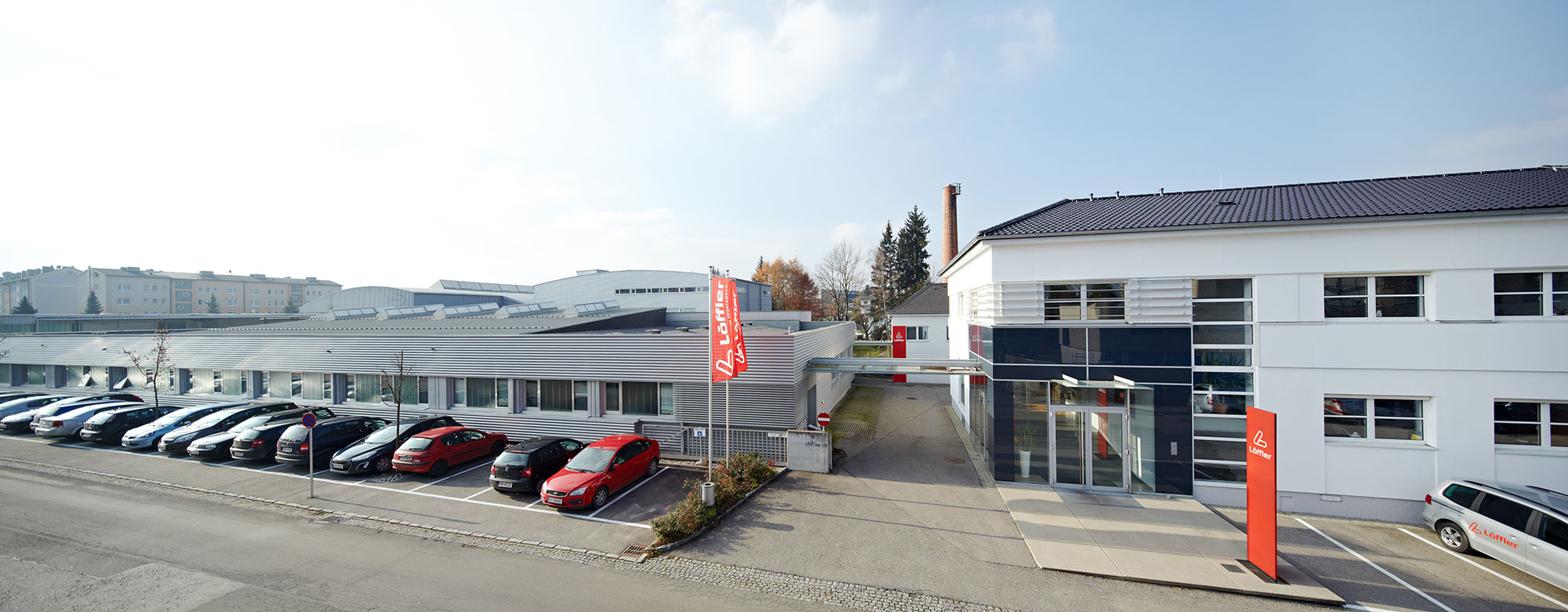
Wie könnt ihr Transparenz sicherstellen für die Materialien, die nicht intern produziert werden?
Derzeit arbeiten wir intensiv an der Transparenz innerhalb unserer Lieferketten. Einerseits soll die Philosophie Löfflers in Bezug auf ökologische und soziale Bedingungen in der Lieferkette definiert werden. Andererseits ermitteln wir gerade, wie weit unsere Partnerunternehmen bereits sind. Welche Maßnahmen und Aktionen werden ihrerseits unternommen? Gibt es bereits bestimmte Standards, Zertifikate, bestehende Audits, und so weiter?
Diese Angaben seitens unserer Partner*innen werden anschließend analysiert und mit unserer Verfahrensweise abgeglichen. Somit kann festgestellt werden, wo Handlungsbedarf besteht. Gemeinsam mit unseren Partner*innen können wir dann die nächsten Schritte festlegen. Es geht also nicht darum, dass wir besondere Standards von unseren Partnerunternehmen „fordern”, sondern eher, diese auf einem gemeinsamen, partnerschaftlichen Weg zu gestalten.
Löffler selbst ist nach dem Standard 100 by OEKO-Tex® zertifiziert und mittels STeP-Zertifikat ausgezeichnet – was wiederum gewisse Standards sicherstellt. Eine Zusammenarbeit mit der Fair Wear Foundation (FWF) ist aktuell in Vorbereitung. Ein weiterer wichtiger Schritt ist die Kooperation mit dem Start-up „retraced“. Dadurch soll die Transparenz entlang der Lieferkette auch für Endkonsument*innen sichtbar werden.
Ist dafür ein Zeitplan einkalkuliert?
Wir sind gerade dabei, die ersten Schritte einzuleiten und das eben erwähnte System zu erstellen, und die Mitgliedschaft bei der Fair Wear Foundation zu beantragen. Wir haben auch gerade angefangen, mit retraced zu arbeiten und unsere interne Datenbank zu füllen. Es ist ein kontinuierlicher Prozess, der nie ganz abgeschlossen ist. Wir haben daher kein fixes Enddatum. In Sachen retraced planen wir zum Beispiel im Laufe des kommenden Jahres auch Ergebnisse auf unserer Website sichtbar zu machen. Ende nächsten Jahres können wir sicher wieder berichten, wie es uns bisher in diesen Bemühungen ergeht.
Letztlich arbeitet ihr oft mit Polyester. Gibt es hier Möglichkeiten, die Rohstoffe länger im Kreislauf zu halten? Ist eure Kleidung zum Beispiel recyclefähig?
Der beste Lösungsweg für nachhaltige Bekleidung ist eine möglichst lange Lebensdauer. Dank der hohen Fertigungstiefe am Firmenstandort in Ried kann Löffler hier an verschiedenen Punkten ansetzen. Durch die zahlreichen Prüfschritte werden nicht nur die inhouse gestrickten Stoffe, sondern auch die Materialien, die wir von Partnerunternehmen beziehen, mehrere Male kontrolliert. So können wir höchste Material- und Verarbeitungsqualität dauerhaft gewährleisten. Um die Lebensdauer dann noch einmal zu verlängern, bieten wir einen hauseigenen Reparaturservice an.
Zusätzlich arbeiten wir an verschiedenen Projekten in Sachen Kreislauffähigkeit. Hier gibt es aber einige Hürden zu bewältigen. Dabei müssen alle Stakeholder beteiligt sein, vom Produzenten über Einzelhandel bis zum Recyclingunternehmen. Auch Konsumierende und politische Entscheidungsträger*innen spielen hierbei eine wichtige Rolle.
Um Bekleidung recyclingfähig zu gestalten, müssen die Materialien unter anderem sortenrein trennbar sein. Das ist oftmals nicht möglich, da Endprodukte meistens aus mehreren Materialien bestehen, die mechanisch oder chemisch getrennt werden müssen. Das ist aber nicht immer machbar. Auch wenn Endprodukte aus Monomaterialien bestehen, müssen trotzdem Fremdmaterialien wie Zipper, Labels, und so weiter, zuerst vom eigentlichen Produkt getrennt werden, ehe sie recycelt werden können.
Ein insgesamt hochkomplexes Thema, mit dem wir uns intensiv beschäftigen und uns laufend mit anderen Stakeholdern – zum Beispiel Recyclingunternehmen – austauschen. Bisher lässt sich keine befriedigende Lösung anbieten.
Die Optimierung der Recyclingfähigkeit ist definitiv ein wichtiger Punkt. Was muss noch passieren, damit die Textilindustrie – und speziell die Sportbekleidungsbranche – wirklich nachhaltiger wird?
Das Wort Nachhaltigkeit ist aus unserer Sicht zu komplex, um hier eine einfache Antwort darauf zu geben. Was wir zum Beispiel machen: Wir haben unseren Nachhaltigkeitsbericht in drei Bereiche gegliedert – ökologische, soziale und ökonomische Nachhaltigkeit. Zu jedem der Bereiche haben wir den aktuellen Status erhoben. Anschließend haben wir uns strategische und taktische Ziele gesetzt und diese mit über 80 Maßnahmen hinterlegt. Zu den Maßnahmen, die bereits erledigt sind, gehören beispielsweise: eine neue, barrierefreie Produktionshalle in Bulgarien, die Kompensation der Treibhausgasemissionen durch den Kauf von Emissionszertifikaten zur Finanzierung von Klimaschutzprojekten, die Erneuerung und Dämmung des Dachs sowie der Austausch der Fenster der Produktionshalle in Ried.
Zu den Maßnahmen, die aktuell noch in Arbeit sind, gehören unter anderem: die Zertifizierung von Löffler Bulgarien nach STeP by OEKO-TEX®, der Umstieg auf Ökostrom in Bulgarien (sofern verfügbar und wirtschaftlich vertretbar), die flächendeckende Umstellung auf Gitterboxen in der Transportlogistik zwischen uns und Partnerunternehmen und damit auch die Reduktion des Bedarfs an Versandkartons. Außerdem möchten wir weiblichen Führungskräfte, insbesondere Gruppenleiterinnen in der Fertigung, durch externe Beraterinnen in Form von Einzel- und Gruppencoaching unterstützen und beraten. Die Entwicklung eines einheitlichen Abfalltrennkonzepts sowie die Einführung an allen Standorten ist ebenfalls in Arbeit.
Diese Maßnahmen und die interne Entwicklung überprüfen wir in vierteljährlichen Workshops und werden dann in unserem nächsten Nachhaltigkeitsbericht dazu Stellung nehmen. Wir sehen, es gibt viel zu tun. Nachhaltigkeit ist ein komplexes Thema, zudem es keine leichte, spezifische Antwort gibt. Alle Stakeholder sind dazu aufgefordert, in ihren Bereichen ernsthaft und mit vielen kleinen Schritten an dem Thema zu arbeiten. Wie wir es zum Beispiel mit unseren bereits genannten Maßnahmen tun. Die Industrie muss sich mit recycelbaren, kreislauffähigen Materialien auseinandersetzen.
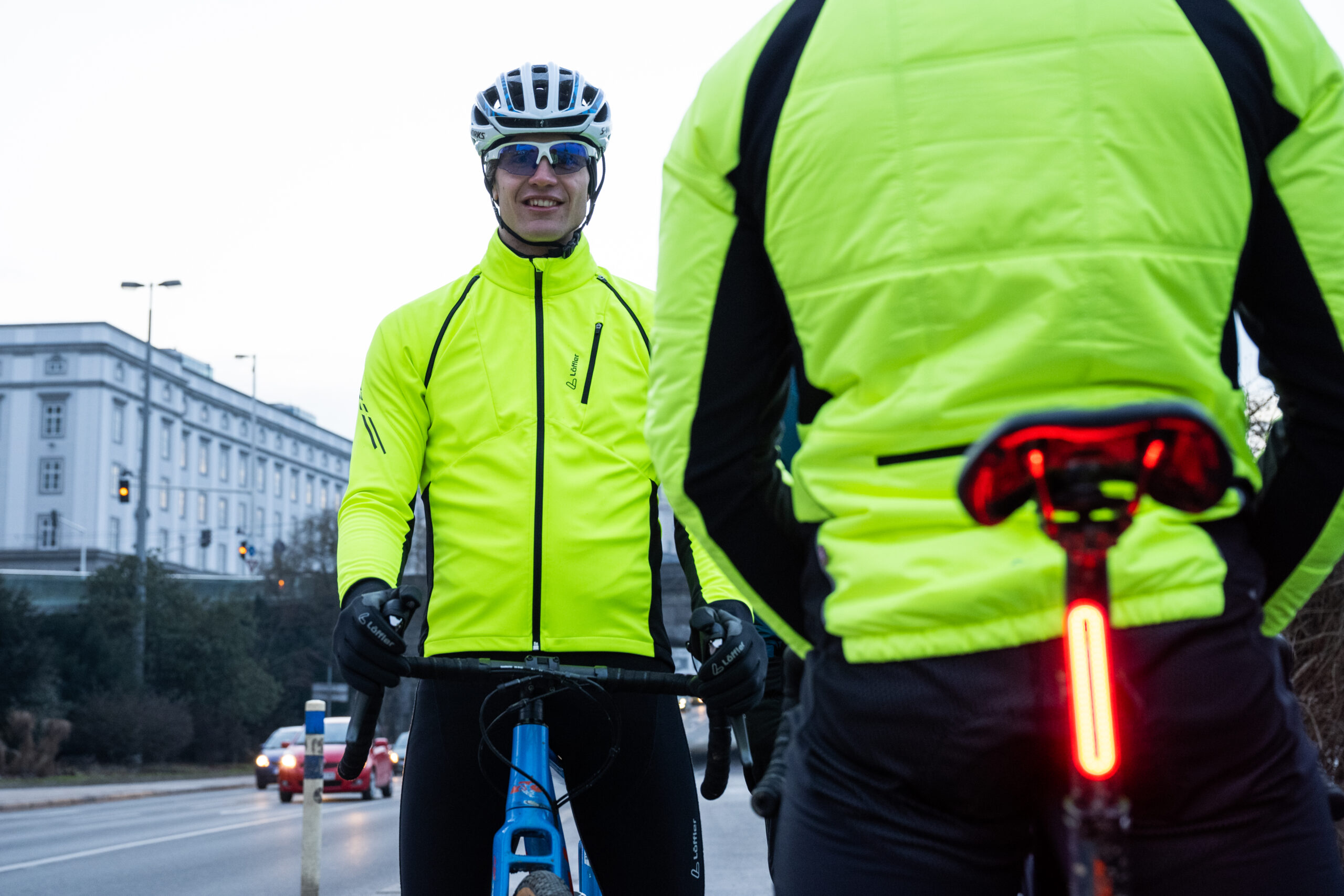
Wichtig ist auch, dass das Thema Nachhaltigkeit in der breiten Bevölkerung eine zunehmende Bedeutung gewinnt und somit der Druck auf alle Stakeholder erhöht wird. Gleichzeitig ist es wesentlich, dass viele Branchenteilnehmer wirklich authentisch, ernsthaft und zielgerichtet agieren. Das bedeutet auch, nicht kurzfristig „grüne Aktionen“ in den Vordergrund stellen, weil das Thema gerade trendy ist. Hier ist also Transparenz gefragt, in Sachen Kommunikation und Lieferketten. Wenn sowohl bei den Produzenten als auch bei den Konsument*innen das Bewusstsein und die Bereitschaft für ernsthafte Nachhaltigkeit steigt, dann könnte sich die angesprochene positive Spirale entwickeln.
Das Problem der verwendeten Giftstoffe
Wie bereits eingangs beschrieben, werden für Sport- und Outdoorbekleidung oft Chemikalien eingesetzt, die für Mensch und Umwelt gefährlich werden können. Eine konventionelle Regenjacke zum Beispiel ist häufig mit einer Lage aus perfluoriertem Chemikalien beschichtet, damit sie wasserabweisend wird. Perfluorierte Chemikalien können in Kläranlagen jedoch nicht abgebaut werden oder reichern sich im Klärschlamm an. Wenn dieser dann in der Landwirtschaft genutzt wird, sickern die Chemikalien in den Boden und werden später von Menschen und Tieren über die Nahrung aufgenommen. Studien zufolge stehen perfluorierte Chemikalien im Verdacht, verschiedene Arten von Krankheiten und Krebs auszulösen – unter anderem Nierenkrebs und Schilddrüsenerkrankungen.
Wenn die Jacke dann auch noch atmungsaktiv und/oder temperaturregulierend sein soll, wird die chemische Zusammensetzung noch komplexer – und somit meistens noch giftiger. Zinnorganische Verbindungen werden zum Beispiel in Socken und Schuhen verwendet. Als Biozid und Anti-Schimmelmittel verhindern sie Gerüche und wirken antibakteriell. Jedoch gibt es Hinweise, dass bestimmte Organozinnverbindungen unter anderem fortpflanzungsgefährdend sind. Der Einsatz einiger dieser Verbindungen ist in der EU deshalb limitiert.
Gerade deswegen ist es immens wichtig, dass sich Unternehmen Gedanken über die verwendeten Materialien machen. Wo kommen sie her? Und wie werden sie produziert? Dass dieser Prozess nicht einfach ist, zeigen die Herausforderungen, die Löffler beschreibt. Unternehmen wie Löffler zeigen aber auch: Eine Veränderung ist möglich, wenn der Wille da ist, Verantwortung zu übernehmen und Stück für Stück die eigene Produktion nachhaltiger zu gestalten.
Löffler hat zwei eigene regionale Produktionsstandorte in Österreich und Bulgarien. Mit Erfolg: Seit 1982 hat LÖFFLER durchgehend Gewinne erwirtschaftet. Der Gesamtjahresumsatz beläuft sich auf rund 28 Millionen Euro. Das Unternehmen beschäftigt 310 Mitarbeiter*innen. 90 Prozent der Wertschöpfung findet in Europa statt.